How to design thermoformed automation trays for high-volume products like CGM sensors and autoinjectors
Thermoformed automation trays — also known as work in process (WIP) trays — provide healthcare and pharmaceutical companies with a critical tool during the manufacturing and distribution cycle. These trays are designed to integrate seamlessly into the manufacturer’s automated equipment while protecting sensitive and high-value components. Several considerations inform the custom design of thermoformed automation trays to ensure optimization.
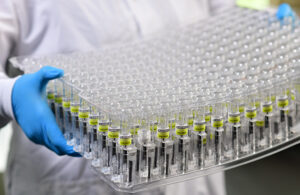
A less common vertical automation tray firmly holds syringes and stacks with a 180° rotation for increased packing density. [Photo courtesy of Plastic Ingenuity]
Product orientation and configuration
Successful design of thermoformed WIP trays that integrate with an automated manufacturing system begins with orientation and configuration of the product in the tray. While products are oriented either horizontally or vertically, configuration is more complex. Rotating the product in X, Y, or Z direction may affect tray capacity, material options, or product protection features. These changes may also have implications on downstream processes like stacking and cartoning. All potential benefits and disadvantages must be considered.
Tray dimensions
Automation tray sizing is determined by several factors, such as the number of parts per tray and the pitch between parts. The automated equipment may also dictate an acceptable length and width for trays. Additionally, it’s important to match the pitch of the end-of-arm tooling, such as suction cups or grippers, and maintain dimensional consistency. Pitch width will change if manual finger picks are needed at any point for loading or unloading the trays. WIP tray sizing also depends on the equipment’s maximum capacity to pick components. For example, if a robot picks 10 components simultaneously, the tray would not be designed in rows of 24, but in rows of a multiple of 10.
Component fit and protection
Properly designed WIP trays provide the required protection for delicate healthcare product components, including clearance from other components, other sections of the tray, and other trays. A tray can be designed with a contour or snap fit cavity. Both feature cavities shaped like the product or components, although snap fit trays include undercuts that firmly hold the product in place. When needed, fitting components to the mold side of the part removes varying material thickness across the tray and provides a more consistent fit.
Maintaining a consistent thermoforming process is also important to the cavity fit. Critical features of the tray will require quality checks throughout the supplier’s production run to ensure the tray will function properly within the automated manufacturing system.
Tray stacking
The total stack height of multiple loaded trays is usually determined by carton fit, automation constraints, or weight limits. For instance, automation equipment determines whether loaded trays can be rotated 180° for stacking or if trays must be stacked without rotation. Aggressive undercuts are required for trays unable to rotate for stacking, which also increases tool complexity. Snap fit cavity trays generally stack higher due to the snap features. By contrast, contour fit cavity trays typically decrease the stack height for greater packing density and reduced shipping rates. But they also require an empty tray to act as a lid or a secondary flat lid to be created.

Noticeable difference in packing density of trays that incorporate large undercuts compared to a tray design that rotates for stacking. [Photo courtesy of Plastic Ingenuity]
Automation trays are repeatedly stacked and unstacked throughout the manufacturing, packing, and shipping stages. Designing trays with a dissimilar corner helps operators easily verify tray orientation within the stack is correct. Another way to optimize by design is to downgauge materials where possible and improve the sustainability of automation trays. Thorough prototype testing will be necessary to confirm the final tray is able to withstand the different forces encountered during manufacturing, packaging and transport.
Automation system integration
Some healthcare and pharmaceutical products might be manufactured across multiple facilities. In the case of decentralization, it’s essential for thermoform design engineers to understand the different processes required to build the product as well as specifications of the automated system. Depending on the complexity, certain products or production methods may require multiple automation trays.
For smooth integration of custom WIP trays with automation systems, collaboration is required at all stages of the supply chain, including the device manufacturer, automation fabricator, and thermoform supplier. An optimized automation process supports operational efficiencies and improves the customer experience, ultimately supporting long-term business partnerships.
Source:MDO