Advancing Medical Device Sustainability with Specialty Thermoplastics
Fig. 1 – Exploded view of device housing and lens made with opaque and transparent LNP CRX copolymer resins.
Thermoplastic resins, composites, and copolymers can help the healthcare industry address multiple sustainability challenges. Specifically, thermoplastic materials can help manufacturers develop medical devices that:
-
Feature optimized designs (lighter in weight, smaller in dimensions, with part and function integration).
-
Incorporate bio-based (certified renewable), mechanically recycled or chemically upcycled material content.
-
Offer greater durability to avoid premature replacement and reduce land-filling.
By choosing specialty thermoplastics, device manufacturers can help reduce the environmental impact of their products while gaining plastic’s well-known benefits of expanded design freedom and streamlined, high-volume production of parts compared to metal alternatives.
BUILDING SUSTAINABILITY INTO DEVICE DESIGN
Medical device manufacturers should consider sustainability in the early stages of their product development process. For example, some thermoplastics enable thin-wall geometries that not only reduce raw material usage, but also offer opportunities for part consolidation, space optimization, and faster processing. Thin walls, of course, also enable smaller packaging to reduce cost and waste, lower weight to conserve fuel during transport, and facilitate portability and usability. Thermoplastics such as SABIC’s LNP™ CRX and HPX copolymer resins provide key properties for thin-wall parts, such as chemical and impact resistance, dimensional stability, and high flow.
Another way thermoplastics can support sustainable device design is by minimizing secondary operations that require additional materials and energy. Some specialty materials enable laser welding, which offers robust sealing technology without adhesives and has the potential to streamline manufacturing. Further, as the performance of adhesives may degrade over time, laser welding can provide leakproof, low-stress welds that help improve product durability and extend useful life.
In contrast to traditional vibration welding, which can potentially damage sensitive electronics, laser welding reduces stress on medical devices while delivering high precision. New LNP ELCRES CRX copolymer resins and ULTEM™ resins provide optical properties (i.e., excellent near-infrared (IR) transmission) required for laser welding.
Still another design strategy to enhance sustainability is to choose mono-materials that make recycling easier, as compared to multi-material constructs that may prevent device recycling. Converting to mono-materials offers the potential for easier waste separation to yield more-consistent recycling streams. Furthermore, a laser welded mono-material may be recovered more easily compared to adhesively bonded materials, which use glues that are hard to separate.
A mono-material approach can be facilitated by selecting several products from the same polymer family. A broad portfolio with multiple grades within a similar base resin allows designers to find the right product for each part’s specific requirements while remaining within the same resin chemistry. One example is combining an opaque grade of LNP CRX copolymer with a transparent grade to produce the housing and lens, respectively, for a wireless connected device (see Figure 1). In addition, mono-materials may allow supply chain simplification by combining similar resins from one supplier, compared to disparate resins from multiple suppliers.
REPLACING FOSSIL-BASED WITH CERTIFIED RENEWABLE MATERIALS
The growing array of bio-based thermoplastics can enable device makers to lower the carbon footprint of their products significantly — without compromising quality and performance. Bio-based versions of thermoplastics that are formulated with renewable feedstocks certified under International Sustainability & Carbon Certification (ISCC) PLUS can lower carbon footprint while providing properties identical to those of fossil-based grades.
For instance, a certified renewable grade of LNP ELCRIN CRX copolymer resin can reduce carbon emissions by more than 40 percent compared to its fossil-based equivalent in accordance with ISO 14040/14044 protocols (see Figure 2). Another example is the certified renewable ULTEM resin platform, whose products are certified under ISCC PLUS and are well suited to healthcare applications such as surgical devices and sterilization trays.
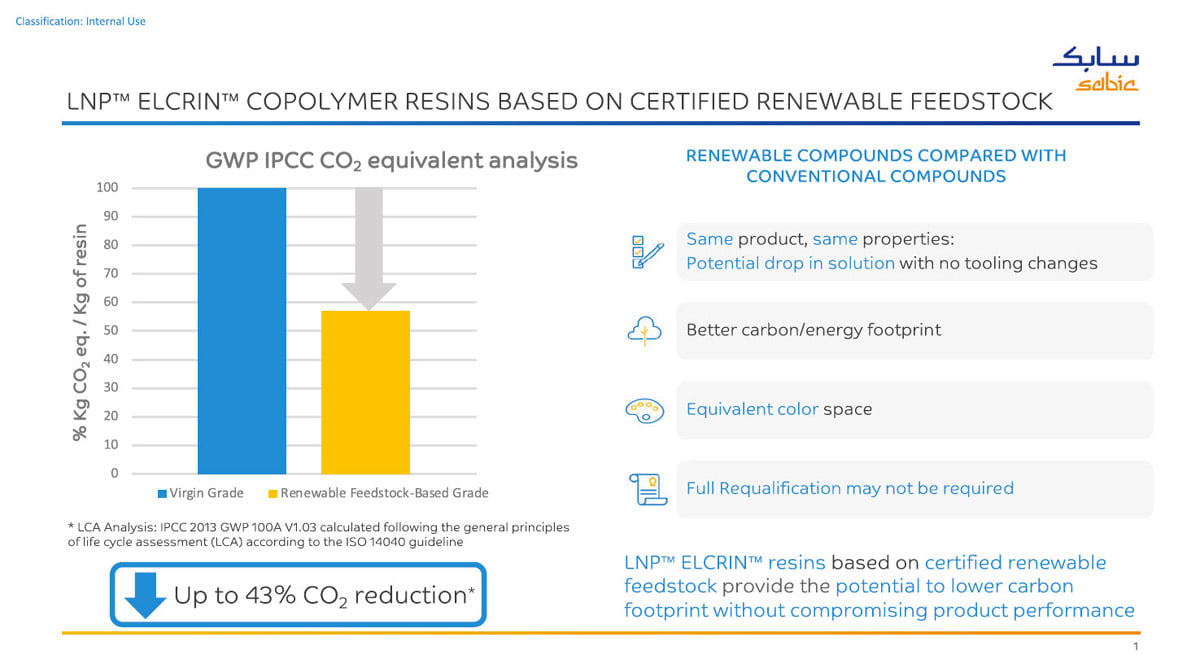
Fig. 2 – Carbon footprint reduction potential with thermoplastic resin formulated using renewable feedstock
Replacing an existing material with a bio-based equivalent should avoid triggering full or partial requalification requirements for regulatory compliance, which can be costly and time-consuming. Suppliers can assist by providing third-party material certification. For example, for flame retardant resins that require Underwriters Laboratory (UL) certification, the UL Solutions Yellow Card for an existing virgin material can be extended to its mass-balanced, renewable feedstock version without any additional evaluation. UL recognizes a renewable grade as chemically equivalent to the same grade produced with fossil-fuel based feedstock. Once UL acknowledges the chemical equivalency, the name of the renewable grade can be added to the Yellow Card of the virgin grade as an alternate designation, or the renewable material can be recognized in a separate Yellow Card with the same UL ratings as the virgin grade.
ULTEM HU1004 resin for medical devices is inherently flame retardant and meets the UL94 V0 standard at 0.75 mm. Because this product requires no FR additives, such as those based on fluorine technology, it can help customers comply with pending regulations on per- and polyfluoroalkyl substances (PFAS).
EXTENDING THE SERVICE LIFE OF DEVICES
While many sustainability initiatives involving plastics focus on recycling, lowering energy usage, and avoiding problematic chemicals, they may overlook the importance of durability. Extending the useful life of a plastic product like a medical device has multiple sustainability benefits. Longer service life means less-frequent replacement, which in turn reduces the consumption of raw materials, energy for manufacturing, and fuel for transport. Longer service life also delays eventual disposal in a landfill or other waste facility.
Thermoplastics can help extend a device’s service life by resisting degradation from disinfecting chemicals, UV light and sterilization, protecting against damage from harsh working environments, and retaining aesthetic properties such as color and surface finish.
Aggressive healthcare disinfectants present a huge challenge to parts such as equipment housings that are made with traditional thermoplastics. Frequent cleaning can embrittle the material, leading to environmental stress cracking and eventual part failure. In comparison, advanced thermoplastics such as SABIC’s LNP CRX copolymers deliver exceptional resistance to alcohols, peroxides, and quaternary ammonium compounds used in healthcare settings. In addition, the new LNP ELCRES CRX products can protect home diagnostic applications such as wearable devices when exposed to harsh chemicals used in sunscreen, hand cream and insect repellent.
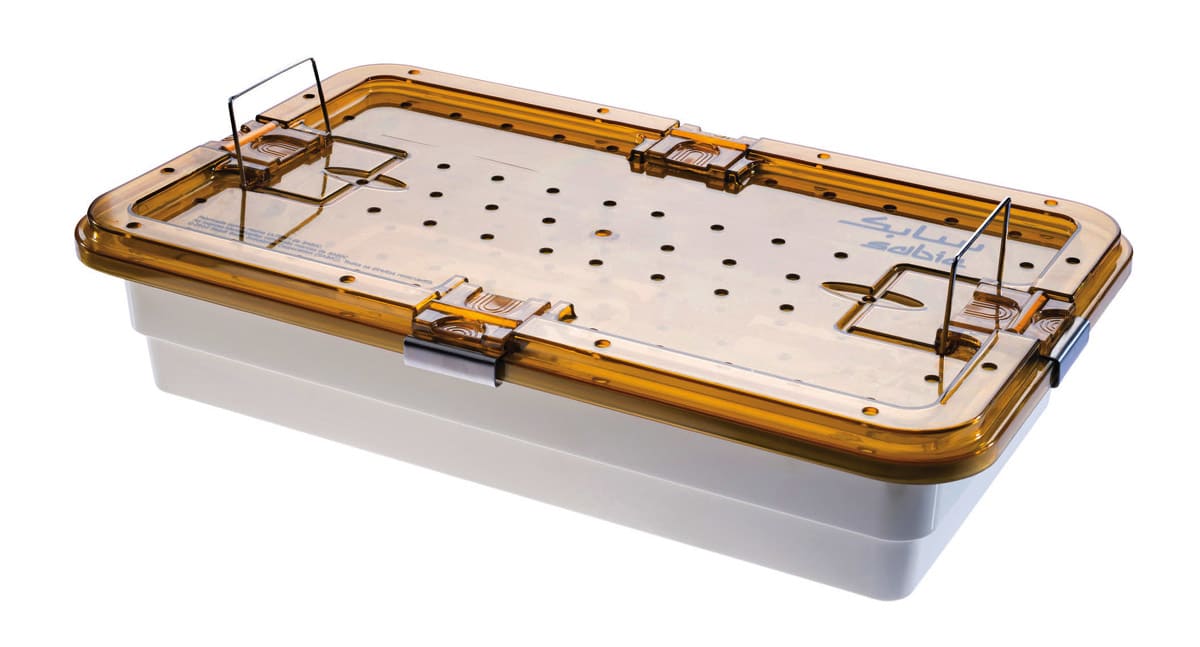
Thermoplastics that can withstand multiple sterilization cycles also help to extend the useful life of devices. ULTEM HU1004 resin maintains its tensile strength, ductility, and color stability in hydrogen peroxide plasma sterilization systems such as STERRAD, as well as gamma irradiation and steam systems (see Figure 3).
Materials with high impact resistance can help prevent damage to expensive devices from being dropped, banged, or mishandled during shipment or everyday usage. Even thin-wall components can resist damage if they are molded from a specialty thermoplastic with enhanced impact properties (a balance of ductility and stiffness).
Many medical, surgical, and dental devices are exposed to strong UV light, which can cause embrittlement, reduced mechanical strength, and discoloration. Wearables such as insulin pumps may also be exposed to outdoor UV light during everyday patient usage. Thermoplastics with good UV resistance can maintain their performance and aesthetic properties under prolonged exposure. ULTEM resin provides up to two times better UV-C resistance than polysulfone-based materials, as well as excellent color retention compared to competitive high-temperature thermoplastics.
CONCLUSION
Medical device manufacturers have many options for improving the sustainability of their products and are under increasing regulatory and reputational pressure to do so. High-performance, specialized thermoplastic materials offer multiple solutions to the challenges of emissions reduction, waste avoidance, and service life extension.
Article Source:Medical Design Briefs