Reshaping Medical Instrument Manufacturing with New Technology
Medical and surgical instruments are utilized daily to save and improve lives. Because of this, they demand an exact level of accuracy and infallibility in their manufacture. Traditionally, aluminum and other metals have been the standard material of choice for medical and surgical instruments due to their weight, strength, durability, and cost benefits. However, new advances in technology are challenging the status quo and offering exciting new manufacturing possibilities that allow for greater material choices. One such advancement already making waves in the aerospace, leisure, and automotive industries — and poised to benefit medical and surgical manufacturing — is Additive Fusion Technology (AFT)™.
AFT™ can utilize materials such as polyetherketoneketone (PEKK) that enable radiolucency for accurate x-ray checks. (Credit: 9T Labs)
ADDITIVE FUSION TECHNOLOGY: WHAT IS IT?
AFT, developed by Switzerland-based 9T Labs, is ushering in a new and emerging standard in hybrid manufacturing for continuous fiber composites. This unique, automated technology outperforms traditional subtractive manufacturing and machined metal components on cost, weight, performance, and sustainability. The platform leverages state-of-the-art integrated software, high-precision additive manufacturing processes, and advanced post-processing to deliver a seamless, three-step solution.
-
First, the software imports computer-aided design (CAD) files for templates while optimizing structural calculations. This means the right amount of material is placed right where it is needed every time.
-
Second, the software feeds this information into a layup/preform machine called a Build Module. The machine’s open material platform begins an additive manufacturing process using two material deposition guides that place thermoplastic filaments (e.g., PEKK, PEI, and PEEK) next to unidirectional (UD) continuous fiber-reinforced tapes (e.g., carbon).
-
Third, a compact compression press fitted with matched-metal dies called a Fusion Module uses heat and pressure to fuse the preform parts and shape them into final parts (with 100 percent traceability and a fiber volume ratio of up to 60 percent in a mold). The process allows for a low void content (< 1 percent), maximum interlaminar strength, metal parts integration, and reshaping.
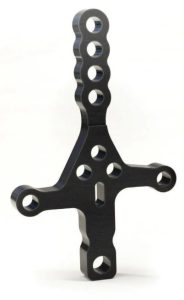
BENEFITING MEDICAL AND SURGICAL INSTRUMENT MANUFACTURING
AFT opens new possibilities for continuous fiber performance when dealing with very intricate and structurally loaded components like the myriad medical and surgical devices that modern, medicine depends upon. This cutting-edge technology can deliver the quick and efficient production of small, strong parts that are not only competitive on cost compared to traditional metal parts, but also represent a new standard for sustainability. For example, it provides a zero-waste benchmark, allows for the manufacture of parts that are resistant to repeated sterilization, and enables the use of materials that can offer end-of-life recycling opportunities without compromising on the mechanical properties of the material.
Additionally, AFT can utilize materials such as polyetherketoneketone (PEKK) that enable radiolucency for accurate x-ray checks, have dimensional stability after repeated sterilization, are biocompatible (since they have short-term contact with the body), and offer low mass for lower fatigue and greater positioning accuracy.
CASE STUDY: SURGICAL AIMING ARM
Surgical aiming arms are used to align surgical tools, pins, and bolts with holes in a bone plate to repair shattered bones while expediting the healing process and restoring mobility. This component was chosen in a feasibility study to examine the impact of AFT on a traditionally machined metal or composite block surgical piece. The company had a goal of developing a design that reduced cost and optimized part geometry. PEKK was chosen because of its better thermal performance and hydrolysis resistance, which is critical given the high heat and humidity of autoclave sterilization for medical devices.
Based on the software design and due to the critical position and dimensional stability of aiming arm holes for positioning surgical tools, aligned fibers (UD tapes) were used to reinforce the holes. The tapes were also used along predicted load paths as well as the external perimeter to strengthen through-thickness resistance to out-of-plane flexure. Additionally, stiff face skins were implemented to create a sandwich structure surrounding the bulk volume of the part, which was filled with unreinforced PEKK. This added step enabled tough exterior surfaces for post-print deburring, polishing, and engraving.
The result is a piece that outperforms benchmark milled aluminum and carbon fiber reinforced polyetheretherketone (CF/PEEK) composite block on cost and weight. Specifically, compared to benchmark machined aluminum, the machined composite parts were 22 percent lighter and the printed AFT parts were 48 percent lighter. The AFT-produced parts also waste 60 percent less material than both aluminum or CF/PEEK, which translates to lower part costs.