3D printing could enable a new cancer treatment
A medtech startup trying to treat skin cancer in a new way used 3D printing to solve a big problem with their tiny device.
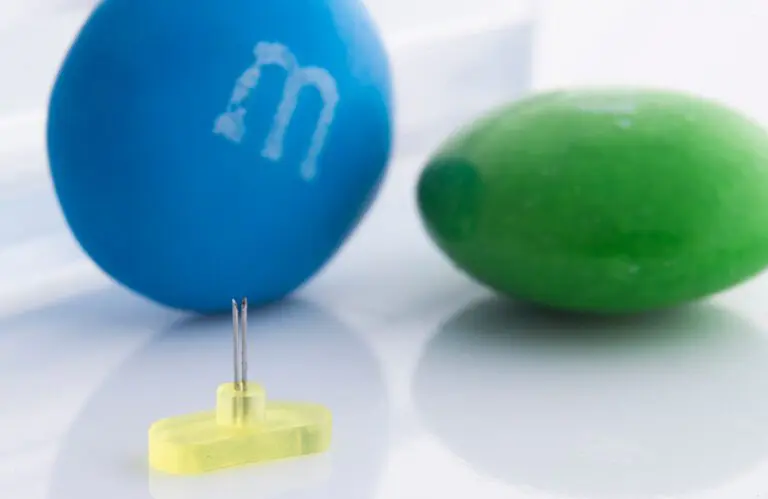
Rotterdam-based Imcomet’s experimental M-Duo technology uses miniature needles to continuously flush fluid through skin cancer tumors: one needle injects the carrier fluid and the other aspirates it, collecting carried fluid plus interstitial fluid and any soluble biomarker molecules that get mixed in.
“The needles stop in the dermis,” Imcomet Chief Technical Officer Alex Motta said in an interview with Medical Design & Outsourcing. “They don’t touch any nerves, they don’t go where there is any blood circulation. You just extract the fluid that is in there and you can get the same as what you have in plasma.”
Worn as a skin patch, this noninvasive method could treat skin cancers by removing the signals that cancer cells use to protect themselves from a patient’s immune system, slowing tumor growth and allowing immune cells to kill the cancer.
Imcomet’s challenge: tiny holes
“Very naively, when we started, we said, ‘OK, we’re going to just take all the technologies that are available, compare them, take the best one, and then just test our hypothesis,’” Motta said. “It turned out very quickly that there was no technology available to do that, so we had to come up with our own way.”
They first tried off-the-shelf insulin needles, but the problem was how to connect even those relatively small needles to microfluidic tubing.
“We started with needles in needles in needles — so a small needle in a bigger needle and a bigger needle,” Motta said. “For our routine experiments, we actually still use the insulin needle in the bigger needle, because I can make them myself. But at a certain point, we needed to go smaller.”
How small? Their goal was to drill two microchannels 20 microns apart from each other.
“Everybody told us, ‘Yeah, we can make very small holes, but that close from each other? Forget about it,’” Motta said.
Imcomet’s 3D printing solution
Imcomet’s solution was a 10 micron 3D printing platform at Boston Micro Fabrication (BMF), which worked with Motta’s team to design and print the device.
“We’re good at making holes,” BMF CEO John Kawola said. “We’re also good at making holes that are very close together, something that’s hard to do with machining.”
A 10 micron platform can typically deliver 50 micron holes or a 50 micron wall, Kawola said. BMF and Imcomet used a light-cured, acrylate-based polymer that meets ISO 10993 biocompatibility standards. After some prototyping and adjustments, Imcomet ordered a batch of 400.
“I’m still living on those,” Motta said. He expects the next order will be a slightly different design based on what his team learned and has planned.
Imcomet said its researchers have already slowed tumor growth in petri dish tests, and that the technology could help treat other cancers and yield samples for proteomic, metabolomic or transcriptomic analysis. The patch could also useful in applications such as diagnostics and drug delivery.
Imcomet Chief Technical Officer Alex Motta [Photo courtesy of Imcomet]The company has one in vitro research machine on the market for customers who want an individually tailored patch with different options such as needle size and length.
Imcomet has also started animal testing and is working toward regulatory approval first as a diagnostic, and then for cancer.
“We have many people interested in clinics for monitoring of patients, for example, sepsis, and for cancer we are teaming up with biomarker discovery companies,” Motta said. “We are not a biomarker discovery company. We just provide access to a new liquid biopsy type.”
Article Source:Medical Design Outsourcing