Pushing the Limits of Possibility in Medical Devices
In 2016, FDA approved Medtronic’s Micra, the first leadless pacemaker to reach the U.S. market. Touted as the world’s smallest pacemaker, the Micra represented a major innovative leap in pacemaker technology. The device is also a frequently cited example of medtech miniaturization.
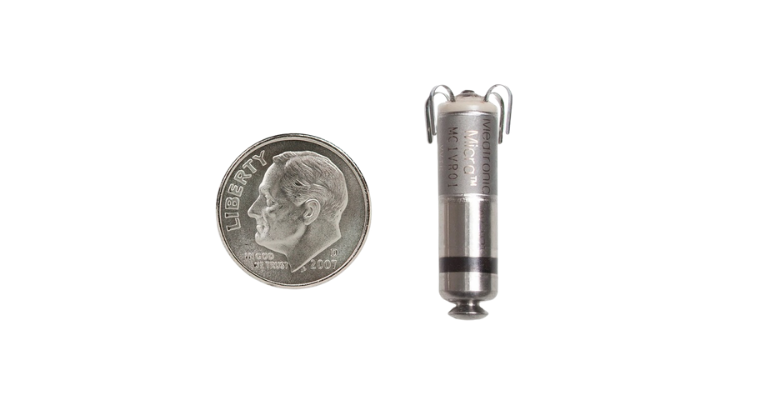
“Over the years, the technology in the medical device industry, especially in the cardiac rhythm management field, has evolved to such that they’re miniaturizing a different product,” said Raghu Vadlamudi, chief research and technology director at New Brighton, MN-based Donatelle. “For example, if we were using a pacemaker, we used to make a lot of micro components for the lead side of the business for that, and now they’re slowly, even on the pacemaker side, they’re making that leadless. So it’s becoming much smaller components, smaller parts, so the micro is getting more prominent because of the need to reduce the size of the devices.”
In 2016, FDA approved Medtronic’s Micra, the first leadless pacemaker to reach the U.S. market. Touted as the world’s smallest pacemaker, the Micra represented a major innovative leap in pacemaker technology. The device is also a frequently cited example of medtech miniaturization.
“Over the years, the technology in the medical device industry, especially in the cardiac rhythm management field, has evolved to such that they’re miniaturizing a different product,” said Raghu Vadlamudi, chief research and technology director at New Brighton, MN-based Donatelle. “For example, if we were using a pacemaker, we used to make a lot of micro components for the lead side of the business for that, and now they’re slowly, even on the pacemaker side, they’re making that leadless. So it’s becoming much smaller components, smaller parts, so the micro is getting more prominent because of the need to reduce the size of the devices.”
Last year, Abbott caught up with Medtronic by bringing its Aveir VR leadless pacemaker to the U.S. market. Boston Scientific is also developing a leadless pacemaker.
Thanks to advancements in miniaturization, leadless pacemakers can be delivered via a catheter and implanted directly inside the heart. Unlike traditional pacemakers, leadless pacemakers do not require an incision in the chest to implant the device or cardiac leads to deliver therapy.
MD+DI has been tracking miniaturization trends for some time, as we’ve seen trends deepen in minimally invasive procedures, wearable devices, advanced drug delivery, and more. We’ve looked at common micro-molding myths, risk mitigation in designing and manufacturing micro-sized devices, miniaturization problem solving, and we’ve shared expert tips for miniaturization R&D. As one expert in the field told us in 2018, any plastic part can be miniaturized, but some are more challenging to manufacture than others, depending on the complexity and geometry of the design.
“The micro side of manufacturing causes a lot of challenges because there is no information that’s readily available when it comes to the small part,” Vadlamudi told MD+DI in a 2021 interview. “The material manufacturers publish processing guidelines for macro parts … so we have information that the materials manufacturer provided to get there faster. But when it comes to micro parts, micro features, there’s no such information available, so most of it is done by trial and error.”
Because there are so few contract manufacturers that dabble in medtech miniaturization, those that do, like Donatelle, tend to keep that information close to the vest, Vadlamudi said. There’s also the fact that every application of miniaturization in the medical device industry is different. Most of these miniaturized parts are molded with implantable-grade PEEK polymer, he said.
“The biggest challenge we see is when we are manufacturing these micro parts, we have to look for machinary, the molding machines, that are suited for these applications. You can’t use a bigger machine to do the smaller part,” Vadlamudi said. “One of the parts that we actually produce in volume is about one-tenth of a milligram in weight. So this part, you can’t even see it unless you put it under the scope. That becomes a little bit difficult to not only mold it but to handle it, to inspect it.”
That means when it comes to manufacturing miniaturized parts, Donatelle has to start thinking on day one about how to handle the part and how to transport it from one location to another as it goes through the manufacturing process to ultimately end up in a device such as the Micra pacemaker. That’s why Donatelle not only manufactures micro-sized medical device components, but the firm also specializes in precision machining, and works with customers from concept to commercialization.
“We actually encourage our customers to talk to us as soon as they get an idea or a concept of it so we can help them in designing those features too,” Vadlamudi said.
That’s advice we’ve heard other micro-molding experts offer as well. Aaron Johnson, vice president of marketing and customer strategy at Ankeny, IA-based Accumold, recommends that engineers start with their ideal in mind. He said he’s often been at a trade show where someone will tell him they’re not quite ready to talk about micro-molding needs yet because they’re still designing their part. But that’s actually the best place to start talking to a micro-molding partner, he said.
“We want you to be able to maximize your creativity, maximize what you’re after through your design, and perhaps there are things you can do that you might not know you can do,” Johnson said during Virtual Engineering Week in 2020. “We love the napkin-sketch idea because we want you to start with your ideal in mind.”
He says he once had a mechanical engineer customer tell him that everything he designs is the size of his monitor.
“It sounds funny, but we’ve seen some incredible designs come across the way, but just because you can draw it in CAD doesn’t mean you can mold it, or just because you can 3D-print it doesn’t mean you can mold it,” Johnson said. “So looking at, what are you after? What is the ideal state that you’re looking for? Then we start looking from there to see how close we can get to your ideal, and in some cases, you might be pleasantly surprised.”
The moral of the story is it’s never too early to start talking with your micro molder about your design, especially as medtech miniaturization continues to advance.
9 Miniaturization myths debunked
1. All micro molded parts are tiny
While some micro molded parts are very small, like the part resting on the pencil shown on the left below, others are larger parts that have microscopic features, like the part around the pencil on the right, Donna Bibber, vice president of business development at Isometric Micro Molding, said during a BIOMEDigital session in 2020.
“This part, about the size of a quarter, is not so obvious that it’s micro,” Bibber said. “However, upon looking at this a little bit further you can see there’s a 250-micron channel that goes all the way down to 3 microns.”
Image courtesy of Isometric Micro Molding
2. Aspect ratios higher than 1:1 are impossible
“This is busted for sure,” Bibber said. “In many of the cannulas and sheaths, for example, that are used in glucose monitoring in diabetes devices are very long and thin.”
3. Tolerances less than 10 microns are impossible to validate to 1.33 Cpk
“We do get a lot of parts that are single micron tolerance, and they’re plastic parts in some cases and other times they’re assemblies or automated assemblies that require these types of tolerances,” Bibber said. “… What we do in the molded part is basically taking each step of your process map and breaking it down to look for microns.”
That process map becomes a living document that the micro molding company uses from quote all the way through validation and production, she explained.
4. Materials behave the same in conventional molding and micro molding
“We know that to be false because we built our own tool based on the ASTM standard tensile bar, which is about 8-inches long, we built our own that’s micro sized, so it’s about the size of the letter I on your keyboard,” Bibber said. “…So the materials behaving the same, we debunked that myth because when you’re going through gate diameters, in our case between 0.006 and 0.013 [of an inch] diameter … so they’re going through this tiny gate and those materials are shearing going through that gate — it’s instantaneous shear but nonetheless it is shear — so it helps us, but in shear-sensitive materials it also hinders us. So it’s really important for us to understand what did we do to the physical properties of the polymer, at least in tensile properties, to understand that emperical data. Before we even build a mold, we can put this in and really understand a lot of different outputs.”
One output would be actual shrink, not estimated, she said. The other output would be gate vestige with actual gate size and material.
“Then, of course, finding out how thin we can go with that material prior to building the real mold,” she said.
5. Wall thickness of less than 0.001 inches are impossible
“We have debunked that because we have this 0.001 tensile bar that we were able to fill with certain materials,” Bibber said. “Now, where this becomes a little bit dicey is when you don’t have a decent melt flow rate, generally speaking, because it’s not all about melt flow rate … but where the rubber hits the road here is melt flow and making sure you have a decent one.”
Bibber said they can also test, by thousandths increments at least, if these can be filled, which she said is very helpful in the medical device sector, particularly in minimally invasive surgical devices.
Where a 0.0005-0.001 [of an inch] increase or decrease in wall thickness makes or breaks a miniaturized design is in things like endoscope distal tips; pressure and temperature sensors; catheters; swallowable, self-steerable devices; dermal delivery; and subcutaneous needle insertion devices, Bibber said.
“All these things have many different parts, all kind of squeezed together in a very small space,” she said.
6. Parts are just smaller, what’s the big deal? Existing tool sources will work just fine
“That is a big mistake that we see. We see parts that have failed and come to us and this is one of the main reasons is the tool,” Bibber said. “The tooling is totally the enabler to doing anything small or precise in terms of micro molding and also in the automated assembly fixture.”
7. All micro molding applications require high injection pressures
“Not true,” Bibber said. “We do have a ultrasonic micro molding machine that we can run 2,000 to 10,000 psi, which might sound like very high, but in terms of micro molding it’s not uncommon for injection pressures to be required at 40,000 to 50,000 psi of injection pressure.”
8. Micro molders are 100% focused on micro molding
“We think we found a good way to debunk that one,” Bibber said. “If that part is held into an end-of-arm tool … we know exactly where those parts are and at what datum structure they are captured into … now, we can let them go, you can put them down and put them into a bulk pack bag, but then somebody has to pick those back up again at some other point and put them together with other parts. What we’ve found is to provide additional value is to put it into a system that has extremely high precision … then we’re solving those yield and quality issues that are associated with manual assembly.”
9. You can’t make it if you can’t measure it.
Bibber said it’s pretty common to hear this statement in miniaturization, but that myth has to go one step further, she said.
“You can’t make it if you can’t validate it,” she said. “Measuring it is one thing, but validating to 1.3 or greater Cpk is very, very important for medical and drug-delivery applications.”