Addressing Challenges in Primary Packaging Testing for Medical Devices
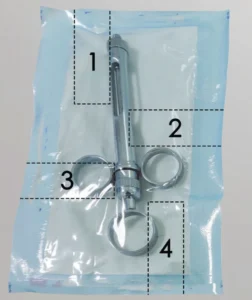
When testing the seal strength of pouches and trays to ASTM F88 or EN 868-5, it is often required to evaluate all 4 edges of the packaging. (Credit: Instron)
In the medical device production environment, device packaging and sterilization is vital. The same level of rigorous quality controls and regulations that affect the devices themselves are also extended to their packaging. The mechanical and container closure integrity [CCI] evaluations of medical device packaging requires significant testing performed at multiple points throughout the commercialization and production processes.
Understanding some of the familiar challenges that can present themselves when performing mechanical testing is vital to developing efficient and repeatable test protocols. In addressing these challenges, the scope of this article includes packaging formats such as pouches and trays, multiple parts of the testing procedure, and distinct stages of the commercialization process.
SPECIMEN PREPARATION
When identifying the most common bottlenecks in the testing process, discussions with medical device companies uncovered that the testing itself was in many cases a secondary concern to specimen preparation. When testing the seal strength of pouches and trays to ASTM F88 or EN 868-5, it is often required to evaluate all 4 edges of the packaging as seen in Figure 1, effectively quadrupling the number of specimens required. The standards provide little guidance for methodology on how to prepare specimens, resulting in variation across the industry. Techniques can range from manually using knife edges or scissors to sample cutters or manual die presses. The range of techniques can result in variation in the seal width/cross sectional area, the cleanliness of the cut, and the consistency of the cut — all impacting the resulting seal strength. Ideally, all operator influence would be removed from the process avoiding imperfections which can artificially reduce the measured seal strength. The use of a pneumatic die punch is preferred, as it eliminates that influence and provides precision cuts quickly.
Additionally, to improve efficiency, die punches can be developed to cut along all four edges of a package with a single stroke, minimizing preparation time significantly. The main challenge is often supporting a flexible array of packaging sizes, which becomes difficult when the punch is sized to the total package dimension rather than the individual peel specimen. Depending on the number of variations, this can be addressed with either multiple punches or by utilizing a system with adjustability in the individual blade locations. The main drawback to these specimen preparation systems is that they may have more expensive consumables, although additional productivity can offer a better long-term financial incentive.
RIGID TRAY TESTING
The use of rigid trays continues to increase alongside the market demand for minimally invasive devices, which require formed trays to protect catheters and introducers. These trays come in a variety of sizes, some even longer than one meter. Rigid trays can be particularly problematic to prepare since most die punch methods will not work with the complex geometry of the tray. As such, they need to be prepared with more manual processes, many of which can introduce safety hazards to an operator. Manually preparing rigid tray specimens is also considerably more difficult to do repeatably when navigating the cutting device along the backing tray geometry.
In the most recent revision to the ASTM F88 standard, added guidance is provided for alternative testing procedures which minimize the preparation needed and allow for the tray to be kept intact during testing. The preparation only requires cutting the flexible part of the package and peeling it directly off the tray. Interlaboratory studies [RR: F02-2001] performed by ASTM took a first step, evaluating the variation in results when testing both cut specimens and full trays with standard tensile grips. The outcome shows that there is an acceptable level of variation between the two methods, and in some cases even an improvement in repeatability when testing the full tray.
The report acknowledges there is still room for improvement when testing the full tray, with the use of specialized fixtures being suggested to further improve repeatability and ease of operator setup. Recent investigations showed the fixturing requires a mechanism to secure the tray throughout the test and clamp the lip of the tray on either side of the peel test region as seen in Figure 2. This design helps ensure that the load is only applied to peel specimen area and there is no flexing of the tray while under test. This setup additionally reduces the effort of the operator to align the specimen before clamping. The proposed solution also implements features to maximize its flexibility accommodating a wide range of tray sizes and geometry.
AUTOMATION
Validating a packaging system can involve testing thousands of samples, requiring considerable time for specimen preparation, testing, and data analysis. Introducing automation into the testing process can provide major reductions to validation time and help reduce operator induced variability. When looking into automated testing systems, it is essential to determine the following to better specify system requirements: volume, throughput, device variety, specimen measurement, data export, and sample identification formats.
Desired throughput and volume will decide the proper technology for automated specimen handling. Low volumes (30 specimens per sample or less) could use simple single axis actuators and grippers while higher volumes exceeding 500 specimens will require industrial six-axis robots to support the larger racking and achieve the necessary speed. Industrial robots also allow for inlining other parts of the process, including specimen preparation and bar code scanning. Device variety will dictate the flexibility required in both the hardware (for grabbing specimens) and software (used to program the system). The preferred user interface is intuitive enough to allow for making modifications to accommodate different sample sizes without requiring vendor support. Even if not using automation, a testing system with the ability to communicate directly with your MES or LIMS system will mitigate data transfer errors and reduce analysis burdens. To further improve efficiency, invest in bi-directional communication to scan in sample information via bar code and automatically pull the corresponding test inputs and method.
Developing and evaluating primary packaging for medical devices continues to be an area ripe for innovation, with ample opportunity to improve existing processes. Addressing the challenges associated with specimen preparation, rigid trays, and production equipment evaluation can ensure testing protocols and equipment are designed to reduce the burden on operators and meet the demanding timelines of medical device commercialization.
Article source:Medical Design Briefs