Q&A: Material Selection for Thin-Walled Micro-Molded Medical Devices
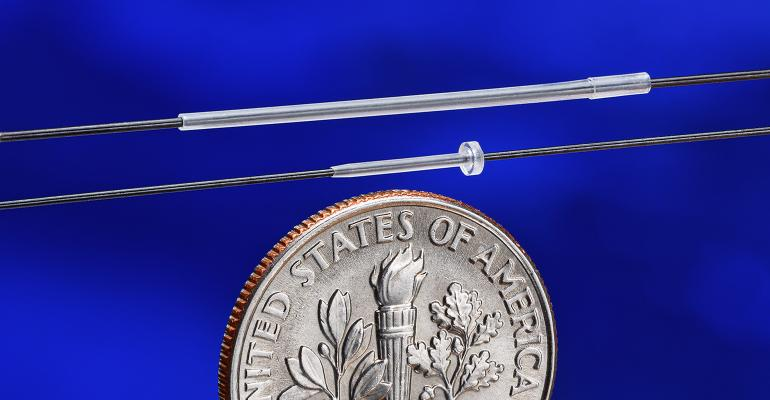
Polymer material selection for thin-walled micro-molded medical products will be under the rhetorical microscope during a session at the co-located Plastec West and Medical Design & Manufacturing (MD&M) West event in Anaheim, CA, next month. Patrick Haney, R&D Engineer at MTD Micro Molding, will discuss the requisite characteristics of various polymer categories to fulfill the demands of thin-wall molding and how to determine the optimal materials for a specific application. He will lean on real-world examples to illustrate his points.
PlasticsToday: In an article on your website, it says that one of the most common questions you hear from medical OEMs is: “How thin can you go?” So, let’s start there: How thin can you go? And what are the primary benefits of thin-wall devices?
Patrick Haney: When it comes to achievable thin walls, the answer is, “It depends.” One of the main factors is material choice. Can your design use a thermoplastic material that is better suited for ultra-thin walls, like liquid crystal polymer (LCP)? Or does your part functionality require other material characteristics, like the rigidity of PEEK, which is much more challenging for thin-wall molding? Or does your thin-wall design require multiple materials for an over-molded component?
LCP and PP are known for their thin-wall molding capabilities, having the ability to fill walls of about 0.002 in., depending on geometry. Polyesters and nylons are also great options.
The main benefits of thin-walled medical device components and implants are patient comfort, and the smaller a part can get, the smaller areas it can effectively monitor and treat. Miniaturization can broaden capabilities of these medical devices, and that goes hand in hand with thin-walled designs.
PlasticsToday: What are the primary considerations when attempting to achieve thin-walled features in a micro-molded part?
Haney: The two primary things to think about are material choice and part design. If you are forced into a material family due to the application of the device, you may be limited in how you can design certain features, like wall thickness.
The other aspect to consider is part design as it applies to injection molding. Ask yourself if you can change part features to better accommodate plastic part design for manufacturability. Although sometimes you are forced to break rules to achieve your goal. For example, if there is a challenging part design that forces a less-than-ideal gating location, that can cause excessive pressure loss or rapid flow front cooling, which can make it more challenging to fill thin walls. Just because you have a material that is best for filling thin walls doesn’t mean it will fill if the design is not optimized.
PlasticsToday: Which medical materials are best suited in these applications, and which ones may be more challenging?
Haney: Materials that are best suited are those that have a more linear polymer backbone. When they are flowing, the degree of entanglement is much less, which promotes lower viscosity. One example is nylon 6/6.
The more challenging materials are those that have higher degrees of entanglement or higher glass transition temperatures and melting points. In other words, it takes more heat to lower the viscosity. An example of this may be polycarbonate.
PlasticsToday: Do material properties change when they are used in micro-molding applications?
Haney: The molding process exposes materials to very high velocities, pressures, and shear rates for a very short period of time. This also means that the cooling rates a material is exposed to are extremely rapid and these conditions can result in unique microstructures that can occasionally affect mechanical and thermal properties. However, with the right tools and knowledge, anticipating that phenomena can result in the material demonstrating desirable properties, as intended.
One of the most common mistakes in micro molding is assuming that non-Newtonian behavior will demonstrate the same characteristics as in macro-molding situations.
PlasticsToday: What other factors should be considered when specifying thin-walled micro parts?
Haney: Considering the final device’s intent and application conditions are really important for micro part design. Some things to consider include, but are not limited to: What is the application temperature? Does the device require any mechanical performance? How long is the device intended to perform its function? These questions are all critical because they may all impact the way the part is designed and manufactured. This is why working closely with your micro molder early about material options and achievable tolerances can set up a project for success.
PlasticsToday: What do you hope that conference attendees come away with from your presentation?
Haney: We want to stress the fact that getting involved with your micro molder as early as possible is in the best interest of the program going as smoothly as possible. There are a lot of questions that need to be answered when designing a device and many materials to choose from. I believe that a little bit of upfront education can go a long way when it comes to giving device designers the knowledge to ask the right questions and better equip them to take their programs in the best direction possible.
Article Source:MDDI